Discovering the Benefits of Fillet Welding in Manufacture: Cost-efficient Solutions for Diverse Industries
In the world of fabrication, the application of fillet welding offers an engaging recommendation for industries looking for economical solutions without compromising structural honesty. The advantages of fillet welding expand beyond mere economic cost savings to incorporate boosted architectural efficiency, flexibility across diverse commercial applications, and the assurance of remarkable toughness and resilience. As we navigate through the practical benefits that fillet welding offers, a deeper understanding arises of exactly how this welding method can reinvent manufacture procedures throughout numerous markets.

Cost-efficient Solution for Fabrication
Fillet welding acts as a cost-efficient option in fabrication procedures, supplying both performance and resilience. This welding technique involves signing up with 2 pieces of metal at an angle, forming a triangular cross-section. The simplicity of fillet welding makes it a popular choice in various markets, including construction, auto, and production.
One of the essential advantages of fillet welding is its capacity to lower material and labor costs. By using fillet welds rather of other complex joint styles, suppliers can conserve money on materials and manufacturing time. In addition, fillet welding calls for minimal preparation compared to other welding techniques, further lowering fabrication expenses.
Furthermore, fillet welds provide exceptional architectural toughness, making certain the long life and durability of the produced parts. The triangular form of the weld distributes tension a lot more uniformly, decreasing the probability of joint failure (Gauge Fillet Weld). This architectural honesty not only boosts the total top quality of the completed product however also minimizes maintenance and repair prices over time
Boosted Architectural Performance With Fillet Welding
Enhancing architectural performance through the application of fillet welding techniques is a critical aspect of guaranteeing optimum performance and toughness in made structures. Fillet welding plays a vital function in boosting structural effectiveness by successfully dispersing lots and stress and anxieties throughout the bonded joints. By producing a smooth transition between the linked parts, fillet welds assist to improve the overall stamina and security of the structure.
One of the significant benefits of fillet welding in enhancing structural performance is its capacity to sign up with products of differing densities. This flexibility enables the building and construction of lightweight frameworks without endangering on stamina. Additionally, the smooth profile of fillet welds lowers anxiety focus, which can aid prevent premature failing of the welded joints.
Moreover, fillet welding makes it possible for the construction of complex geometries easily, offering designers with even more liberty in creating efficient and cutting-edge structures. By maximizing the style and positioning of fillet welds, engineers can optimize the structural performance of fabricated components, eventually bring about cost savings and enhanced efficiency in varied industries.
Flexibility in Diverse Market Applications
With its capacity to deal with a variety of material thicknesses and geometric intricacies, fillet welding stands as a versatile manufacture technique that finds applications across varied industries. One crucial location where fillet welding succeeds is in the production sector, where it is made use of in the manufacturing of heavy machinery, devices, and structural parts. The automobile sector also gains from fillet welding, using it in the setting up of vehicle frameworks, chassis, and various other critical structures. In the construction area, fillet welding plays an essential role in joining steel light beams, columns, and various other architectural components. Furthermore, the aerospace sector relies upon fillet welding for the construction of airplane parts, ensuring stamina and resilience in crucial parts. Furthermore, the oil and gas industry uses fillet welding in the building and construction of pipelines, platforms, and storage tanks, where the robust welds supply integrity and durability to these structures. Generally, the adaptability of fillet welding makes it an essential process in various industries, providing cost-effective solutions for complicated fabrication demands.
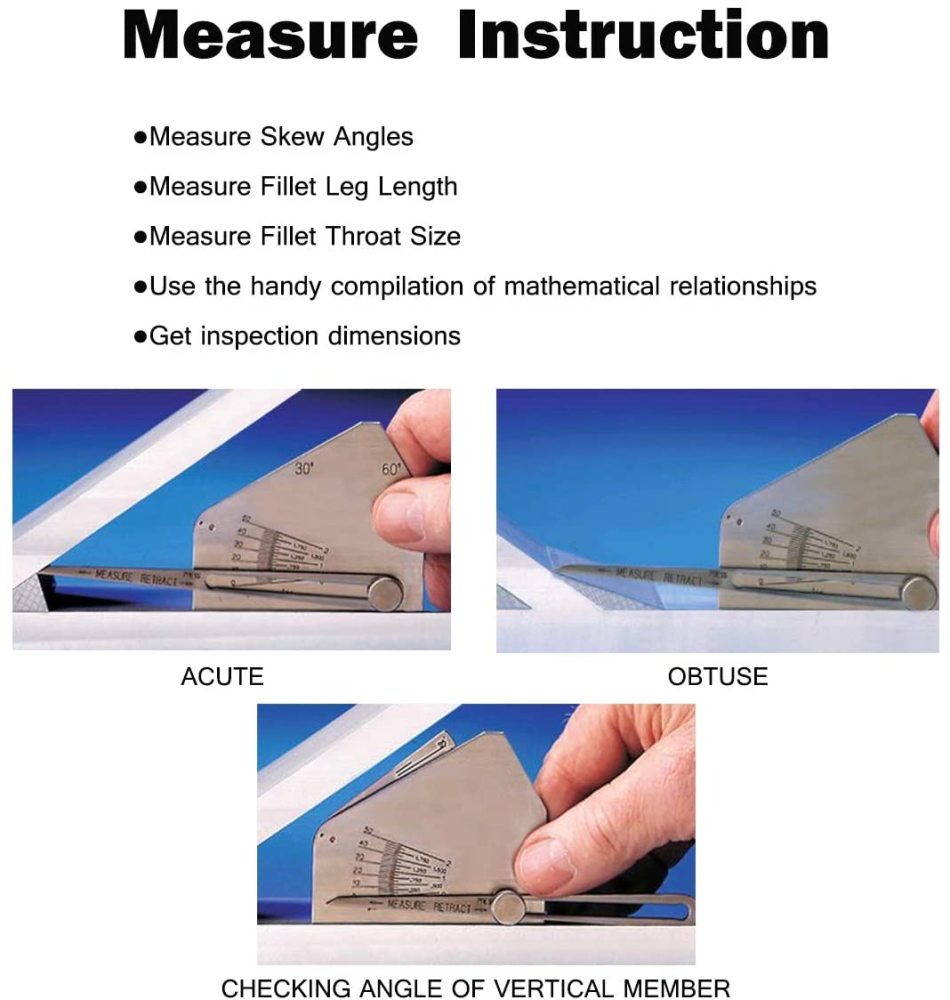
Superior Toughness and Durability
Fillet welding plays a crucial function in achieving these characteristics due to its capability to give considerable strength by distributing lots evenly across the bonded joint. As an outcome, structures produced making use of fillet welds show increased longevity and can stand up to significant mechanical forces without jeopardizing their honesty.
The exceptional stamina and durability provided by fillet welding make it an excellent option for applications in industries such as building and construction, automotive, aerospace, and manufacturing, where architectural integrity is vital. By utilizing fillet welds in fabrication, makers and designers can make certain that their products meet stringent high quality and safety criteria while optimizing cost-effectiveness and manufacturing performance. In significance, the phenomenal durability and long life offered by fillet welding make it a favored welding method for producing sturdy and robust structures across varied markets.
Practical Advantages of Fillet Welding
Given the demonstrated remarkable strength and durability in bonded joints, the practical benefits of fillet welding extend past architectural integrity to include efficiency and cost-effectiveness in fabrication processes. One crucial sensible benefit is the simplicity of fillet welds, which do not require intricate or costly devices to create. This simpleness equates into time savings throughout construction, as fillet welding can be swiftly applied in numerous placements without the requirement for sophisticated setups. In addition, fillet welding enables for enhanced performance as a result of its flexibility in joining various sorts of products, i loved this thicknesses, and forms. The versatility of fillet welds makes them suitable for a vast array of applications throughout varied sectors, better contributing to cost-effectiveness in manufacturing processes. The lowered need for extensive surface area prep work contrasted to various other welding techniques minimizes material waste and decreases production downtime. Overall, the useful advantages of fillet welding make it a valuable selection for business looking for economical and efficient options in construction.
Conclusion
In verdict, fillet welding offers an economical remedy recommended you read for fabrication, providing boosted structural efficiency, versatility in varied market applications, remarkable strength, and toughness. The useful benefits of fillet welding make it a preferred option for numerous fabrication jobs across different markets. Its capacity to effectively sign up with materials while maintaining structural stability makes it a valuable strategy for making certain top notch and trustworthy cause welding applications.
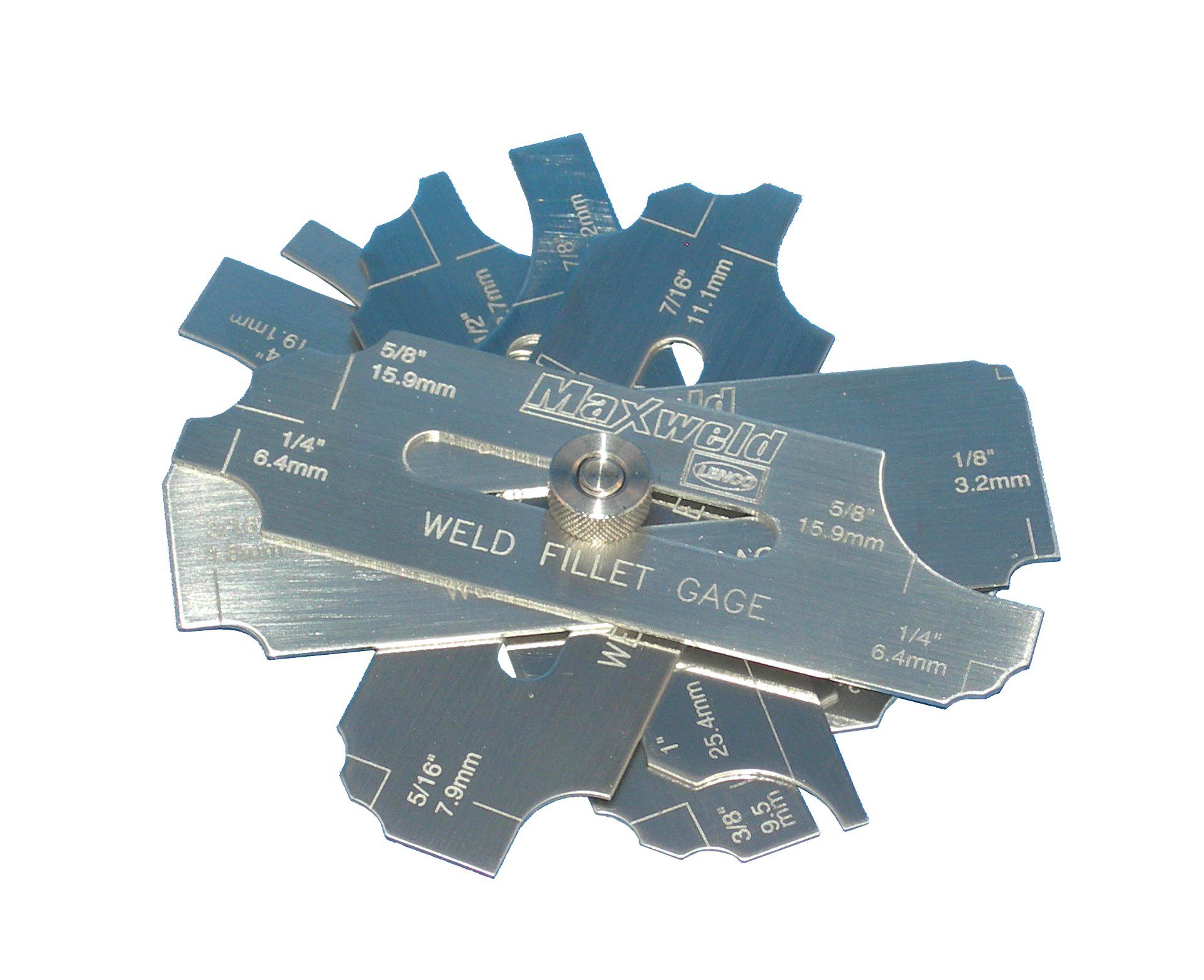
Additionally, fillet welding requires minimal preparation compared to other welding techniques, even more lowering fabrication costs.

Provided the shown superior strength and resilience in welded joints, the practical advantages of fillet welding expand past architectural honesty to encompass performance and cost-effectiveness in construction processes - Gauge Fillet Weld.In final thought, fillet welding supplies an affordable remedy for fabrication, providing enhanced architectural performance, versatility in diverse market applications, premium strength, and sturdiness
Comments on “How to Accomplish Precision with Gauge Fillet Welds in Your Jobs”